How Does A Volumetric Concrete Mixer Work?
Each material is loaded into individual compartments. Cement can be loaded by bags, super sacks, or from a silo. Aggregates are typically loaded with a skid steer or a front end loader. Water can be loaded from the top of the unit or from a deck mounted port. Each liquid admixture is also stored in its own tank and dry admixtures have a separate container.
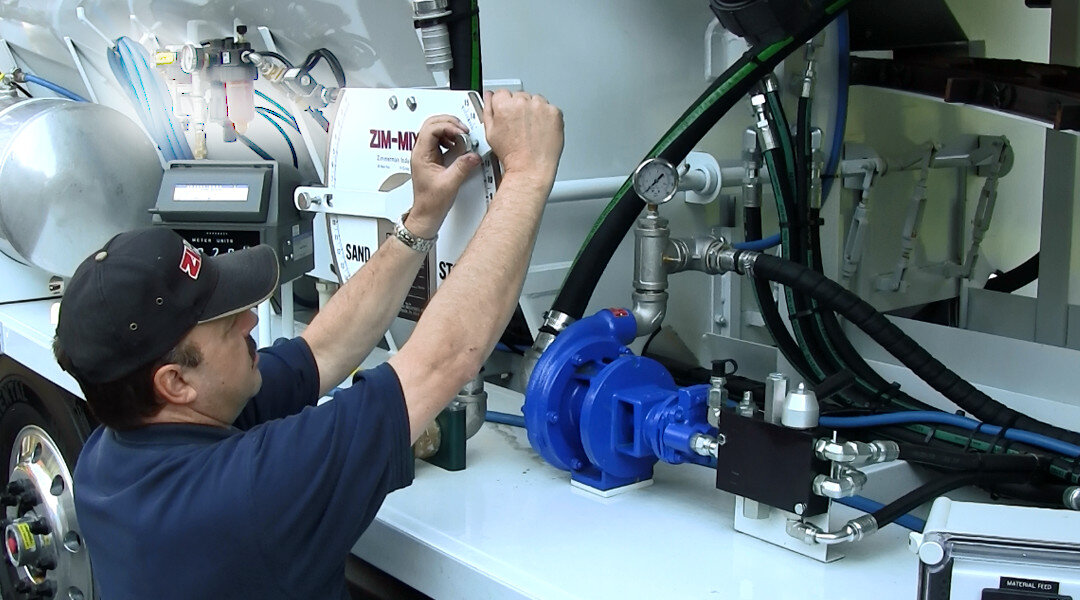
Independent fine and coarse shutter gates are used to accurately proportion these materials, once calibrated. Each delivery system has been certified to meet the ASTM C685 requirements. Different settings are used to produce specific mixes and can be adjusted on site to meet the customer’s requirements.
The operators control panel is located at the rear corner of the machine, allowing for all of the mechanisms to be observed from one place. Each of the systems is activated from this spot, permitting the operator total control of the process.
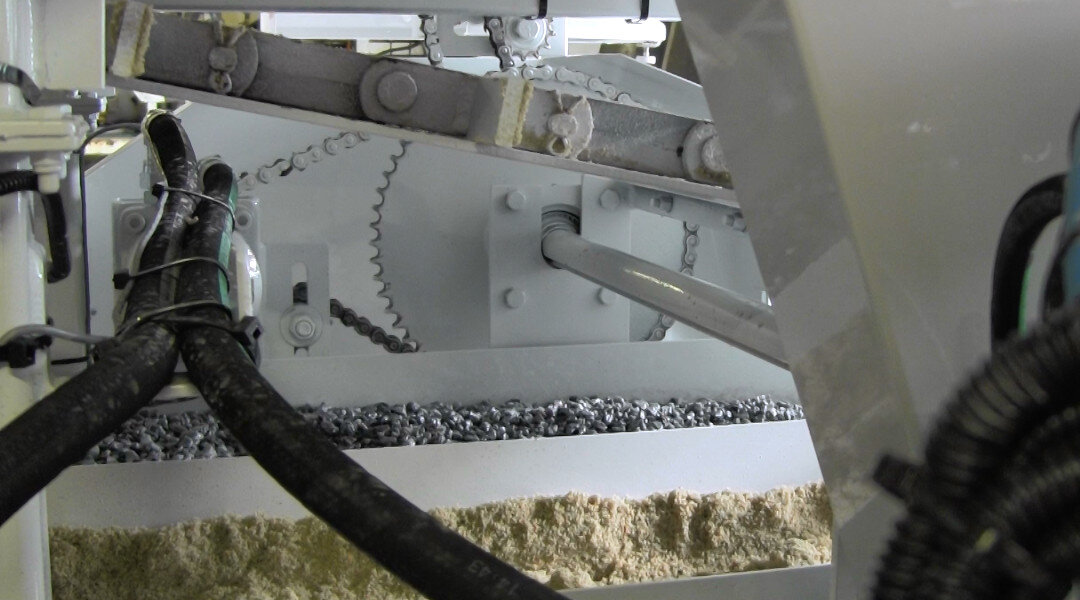
Our patented chain feed delivery system is a positive drive mechanism that accurately and consistently delivers the dry materials to the mix auger. The Zim-Mixer is the only machine that allows for all of the ingredients, dry or liquid, to be run individually while loaded, enabling the mixer to be quickly and easily calibrated as well as off loaded without cross contamination. Our patented system also allows sand, stone, grout, or even pervious concrete to be delivered or produced at any time.
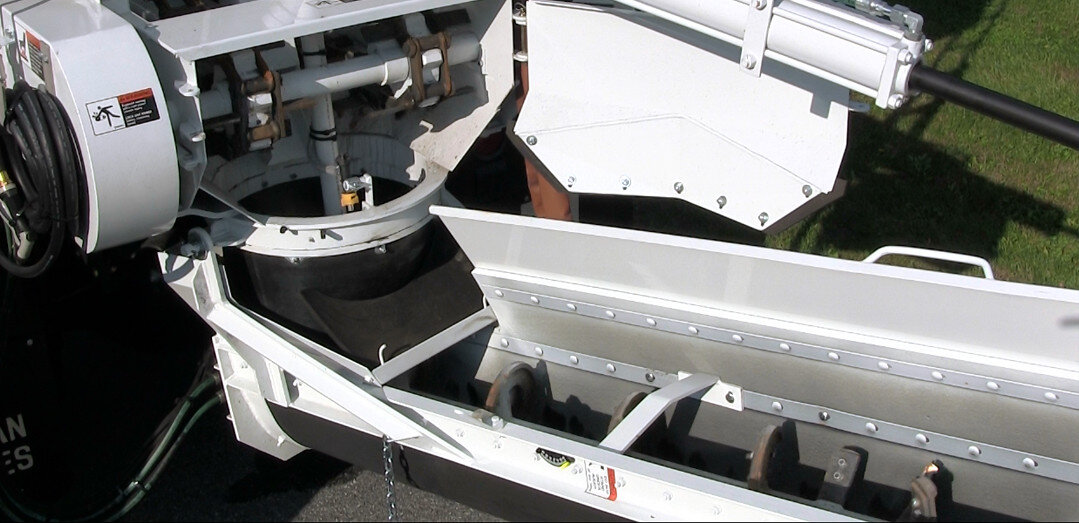
All proportioned materials are brought together at the auger hopper, where the mixing begins. As the materials are continuously fed to this area, the mix auger blends and mixes them into a homogenized product. Mixing paddles along the auger flighting aid in producing thoroughly blended materials.
The material delivered from your Zim-Mixer has been accurately proportioned to the exact fresh mixture required, and in the exact amount desired. Our auger positioning controls and chute options allows the operator to precisely place the material without additional labor.